DLC Coatings for Handguns
Firearms are tools subjected to significant mechanical and thermal stress. Combined with harsh usage conditions, this can lead to rapid wear and loss of functionality, especially when improper cleaning and maintenance are applied.
The industrial tool industry has faced a similar challenge with wear and tear since its early days. To slow down tool wear, various coatings have been used for many years, including FNC (Ferritic Nitride Coating) or Titanium Nitride (TIN). These coatings must demonstrate several extreme properties such as high hardness, resistance to shear, bending, cracking, and good adhesion to the coated surface.
For this reason, the DLC coating (from English, Diamond-like Carbon) has gained increasing popularity in recent years. In Polish technical terminology, it is referred to as diamond-like carbon coating. This coating was first applied on a wide scale in the aerospace and automotive industries for coating tools and the most sensitive moving surfaces. It is no surprise, therefore, that leading firearm manufacturers are now adopting DLC coatings in their designs, especially in handguns such as Glock and Bul.
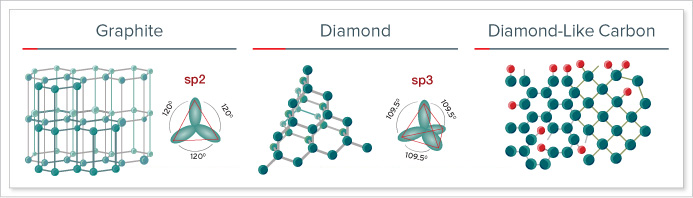
The English name is by no means exaggerated, as the properties of the coating demonstrate this. DLC combines the advantages of two carbon fullerenes – graphite and diamond, resulting in high surface hardness and thermal conductivity, along with the resistivity of diamond and lubricity and electrical conductivity of graphite.
According to one of the coating manufacturers, their surface hardness reaches 2800 – 3800 Vickers scale, which is a tenfold improvement compared to uncoated steel. The friction coefficient (or smoothness) of the DLC IHC coating ranges from 0.04 to 0.15 CoF, compared to most steels, which range from 0.50 to 0.60 CoF in non-lubricated environments. What does this mean? It means that, compared to conventional steel parts, we achieve a 5-10 times reduction in wear.
Another advantage of DLC coatings is the reduced need for lubrication of the firearm. DLC coatings are naturally very smooth, and since the layers are completely dry after application, contaminants and residues from propellants slide off rather than sticking to the surface.

Most importantly, DLC coatings do not affect the operation of the firearm’s mechanics, as they are applied via chemical vapor deposition. This allows for perfect adaptation of the coating to the shape of the substrate, in this case, the varied dimensions of the firearm’s internal parts.
Currently, the only mass producer that has made DLC coating a standard is Glock, with its version – nDLC – coating the fifth-generation pistols of the popular Austrian manufacturer. In the Polish market, Bul also offers DLC coating as an upgrade for their custom handguns. The price may seem high – 1700 PLN for coating the slide, frame, and barrel, and 1800 PLN for coating the entire pistol. However, we must remember that these pistols – especially competition models – will fire thousands of rounds. Many shooters treat the purchase of a firearm as an investment – coating the pistol, which reduces wear several times over, can be a great way to safeguard that investment.
Pistols from the SAS II series by the Israeli manufacturer Bul will particularly benefit from the DLC coating – it is expected that they will fire many thousands of rounds.